Une polémique absurde et même indigne s’est installée autour du livre de Fabien Roussel sur le travail. Pourtant ce livre et ce sujet devrait permettre d’ouvrir la discussion non seulement sur les exigences populaires mais sur le sens de l’industrialisation nécessaire de la France. J’espère que dans son livre Fabien Roussel consacre une réflexion à la planification. S’il est une leçon à tirer de la Chine c’est à quel point le développement actuel de l’industrie a besoin d’une planification pour en intégrer les différentes étapes dans un continuum. L’industrie du futur, celle de la révolution numérique ne saurait se passer d’aciéries et d’autres fondamentaux, pour avoir les formations nécessaires et pour concevoir ces formations dans un développement des individus qui exige une politique du logement, de l’éducation, de la recherche, et concevoir que tout cela ne peut exister sans une réflexion sur les salaires et sur les coût des services. L’humain d’abord cela ne se fera pas sans l’entreprise et ses salariés mais pas sans intégrer ce collectif dans la planification nationale et ses priorités qu’il faudra bien imposer à la logique de rentabilité de l’entreprise même améliorée par de nouveaux critères de gestion. (note de Danielle Bleitrach pour histoireetsociete)
Par Laura Lamassourre • Publié le 13 février 2025 à 12h02 • Sponsorisé par Siemens France
Deux experts de Siemens nous éclairent sur l’industrie d’aujourd’hui et de demain.
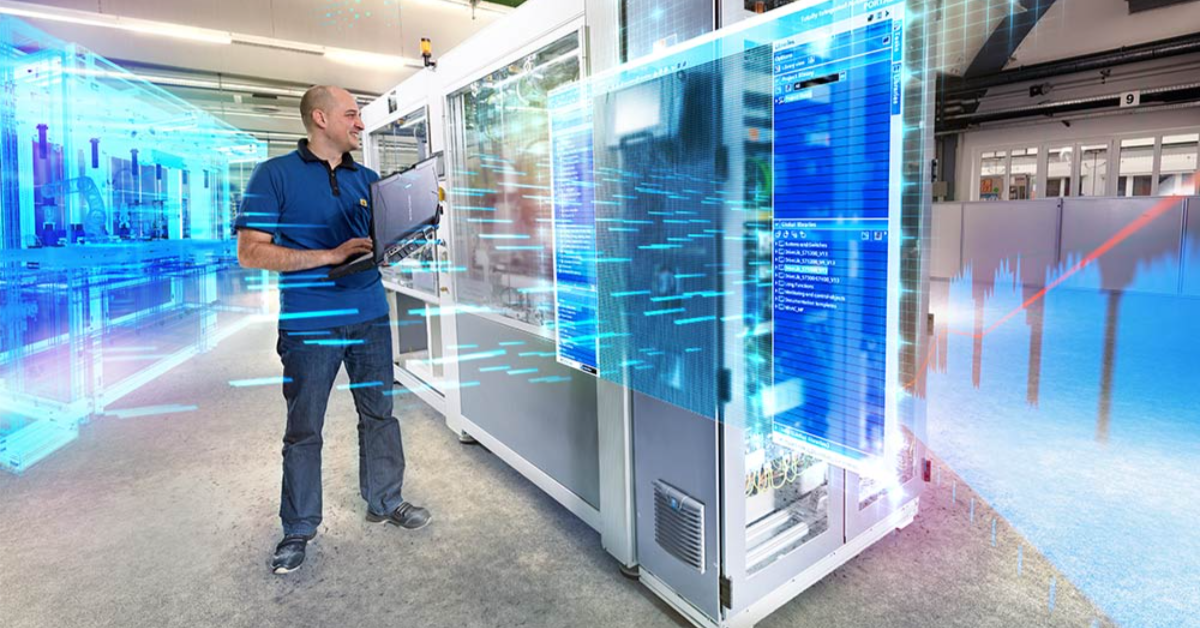
La politique de réindustrialisation tricolore est un axe stratégique pour la France. Dans l’hexagone, l’industrie représente plus de 7,6 millions d’emplois directs ou indirects, selon les chiffres clés 2024 de France Industrie. Un secteur dynamique qui tente de mener, de concert, sa transition écologique et sociétale. Pour Stéphanie Lakkis, General Manager Factory Automation chez Siemens Digital Industries France et Yohann Mesmin, Responsable Business Development chez Siemens Digital Industries Software, la clé de ce succès sera numérique.
De nombreux industriels parlent aujourd’hui de convergence IT/OT (informatique d’entreprise/informatique industrielle) : l’intégration de données provenant des machines qui gèrent des informations variées sur la production, combinées à la data issue de systèmes de surveillance et de contrôle de la production. « C’est à la fois un lien entre le monde réel et le monde virtuel, et une connexion forte entre les différents acteurs d’une entreprise. Notre rôle est de faciliter cette convergence et de faire dialoguer et se rencontrer ces deux mondes avec un objectif commun d’amélioration de la performance », éclaire Yohann.
« Bâtir un avenir bas carbone et résilient »
Avec son équipe, Yohann promeut l’ensemble de l’offre de transformation numérique proposée par Siemens. « Nous collaborons avec tout type de secteurs et d’acteurs industriels, de la start-up au grand groupe. Notre but ? Les convaincre que l’innovation passe par la transformation numérique », explique-t-il. Stéphanie et ses équipes se consacrent à l’automatisation et ont en charge les verticaux manufacturiers : « Nous proposons des solutions d’automatisation pour la fabrication industrielle et accompagnons le développement des industries manufacturières. Nos domaines d’activité couvrent des secteurs variés et passionnants, de l’agroalimentaire et l’automobile à la production de batteries et de semi-conducteurs, en passant par les infrastructures, l’énergie et le recyclage. »
Stéphanie Lakkis
General Manager Factory Automation chez Siemens Digital Industries France
Ensemble, ils automatisent et digitalisent les sites de production industriels. Des enjeux qui s’inscrivent dans les défis globaux du secteur. « L’industrie française doit concilier compétitivité, transition écologique et transformation numérique afin de bâtir un avenir bas carbone et résilient. Cela passe par des chaînes de production plus efficaces et plus respectueuses de l’environnement », soutient Stéphanie.
Pour y parvenir, l’intégration de technologies adaptées à ces défis est essentielle, qu’il s’agisse de décarbonation ou de digitalisation. « Ces technologies doivent également permettre l’optimisation, car les industriels restent constamment focalisés sur leur performance. Avec de nouvelles méthodes et un nombre croissant de machines connectées, d’automatisation, de digitalisation et de robotisation, nous faisons face à une multitude de données qu’il faut désormais exploiter », continue-t-elle.
« Les métiers de l’industrie sont accessibles à tous les profils »
Yohann identifie deux autres défis majeurs de l’industrie : « Maîtriser son écosystème de fournisseurs et toute sa chaîne d’approvisionnement. C’est absolument nécessaire dans un contexte de devoir mieux comprendre et optimiser son empreinte carbone. »
Yohann Mesmin
Responsable Business Development chez Siemens Digital Industries Software
Le second ? « Contrôler les cycles de développement produit, du début à la fin, répond-t-il. Pour être compétitif, les industriels doivent être meilleurs que leurs concurrents et, à cet effet, innover plus rapidement. Notre but est de les accompagner et de leur offrir des solutions pour accélérer leur time to market (NDLR : le temps entre la conception d’un produit et sa mise en vente). »
Autre enjeu pour l’industrie : redorer son image auprès des candidats. « Nous pensons qu’il est essentiel de travailler collectivement à cette image afin d’attirer et de retenir les compétences nécessaires au développement de l’industrie, souligne Stéphanie. Cela passe par la formation et l’accessibilité des sites industriels, permettant ainsi de se projeter dans des domaines stimulants ! » Un point de vue partagé par son collègue : « Les métiers de l’industrie changent. Ils sont accessibles à tous types de profil, féminins comme masculins. »
« Grâce à notre expérience industrielle, on peut approuver nos technologies »
Côté développement numérique, les solutions sont nombreuses pour l’industrie. Et l’intelligence artificielle (IA) n’a pas le monopole du sujet. « Nous entendons beaucoup parler d’IA, comme si elle allait tout changer, commente Stéphanie. Il y a effectivement une vraie révolution qui s’opère avec l’IA, en disruption avec la manière d’amener des solutions sur les sites industriels, mais énormément d’enjeux technologiques actuels n’intègrent pas de machine learning * ou d’IA. »
Doté de plus de 120 usines à travers le monde, Siemens éprouve de nombreuses technologies et apprend des données récoltées. « Grâce à notre expérience industrielle, nous pouvons dupliquer nos technologies une fois approuvées, les dupliquer et accompagner nos clients dans la maîtrise de la donnée », ajoute Yohann.
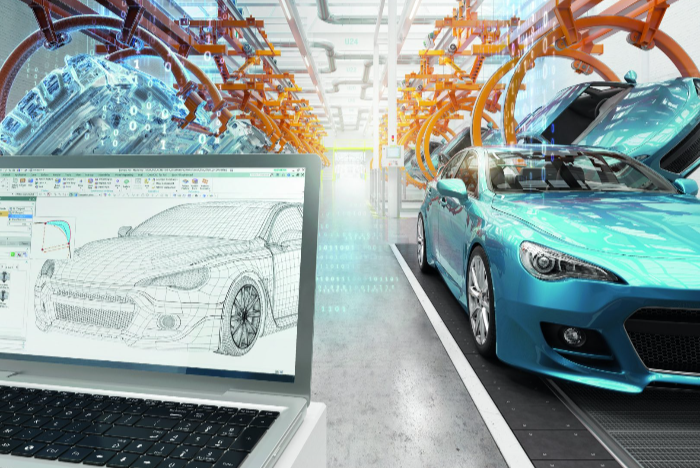
Les machines connectées ou objets IoT ** en sont un des piliers. « Cela sous-entend une exposition à des cyberattaques, des vulnérabilités par exemple. Chez Siemens, nous travaillons sur des technologies de cybersécurité robustes, des produits et des protocoles renforcés pour protéger les données et les systèmes critiques », explique Stéphanie. Le hic ? La majorité des sites industriels mixent des technologies anciennes et d’autres, plus récentes. « Cette hétérogénéité des systèmes rend parfois l’intégration des technologies connectées difficile. Nous avons donc lancé Xcelerator, une plateforme ouverte, évolutive et interopérable. Elle permet aux entreprises d’intégrer de manière simplifiée le matériel, les logiciels et les services numériques, les aidant ainsi à devenir plus flexibles, efficaces et durables », détaille-t-elle.
« Créer des lignes de production grâce à des outils digitaux »
Siemens possède un important catalogue de solutions pour ses clients, quel que soit leur secteur industriel. « Il n’y a pas que l’industrie automobile et aéronautique ! pointe Yohann. Nous travaillons aussi avec l’industrie médicale, agroalimentaire, la chimie, la pharmacie ou encore l’électronique. » Un tel portefeuille de solutions permet notamment à Siemens de répondre aux besoins de jumeaux numériques. Un digital twin est une représentation virtuelle d’un objet, une opération ou un système. Il accompagne le produit tout au long de son cycle de vie, il est dynamique et est mis à jour à partir de données en temps réel, et s’appuie sur la simulation et le machine learning, il doit aider à la prise de décision et à l’analyse de la performance.
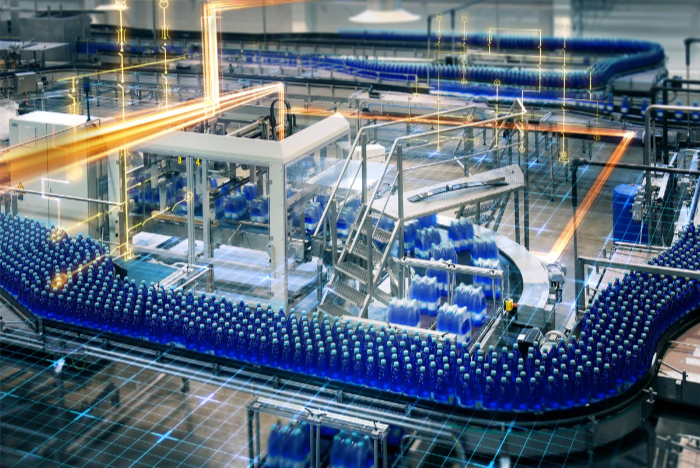
Un exemple : l’industrie de la chaussure, et plus particulièrement de la basket. « C’était une industrie que nous avions perdue face à la concurrence asiatique. Grâce à un modèle d’usine 4.0 intégrant de nombreuses technologies telles que réalité augmentée, jumeau numérique, robots autonomes, nous avons aujourd’hui la capacité de concevoir l’usine qui accueillera le produit une fois qu’il est pensé. Nous sommes donc capables de créer des lignes de production grâce à des outils digitaux combinés à une automatisation très avancée ! » souligne Stéphanie.
« Qui dit intégration de nouvelles technologies, dit évolution des profils »
Pour mener à bien tous ces projets, l’industrie s’équipe de nouveaux profils et forme ses collaborateurs. « Nous allons retrouver des data scientists, des experts en robotique et en intelligence artificielle, des consultants en technologie, ainsi que des développeurs, par exemple. Étant donné que nous évoluons dans des systèmes interconnectés, les compétences deviennent de plus en plus transversales, avec un besoin « terrain », allant de l’approvisionnement au produit fini. L’intégration de nouvelles technologies entraîne donc l’évolution des profils », relève Stéphanie.
Siemens mène également des projets avec des partenaires technologiques. Une initiative qui pourrait intéresser de nouveaux profils de collaborateurs. « Nous venons par exemple de lancer un casque de réalité virtuelle en collaboration avec Sony, destiné au secteur industriel. Ces évolutions et innovations pourront notamment attirer les joueurs de jeux vidéo, qui retrouveront des fonctionnalités proches de leur quotidien dans leur métier », développe Yohann.
Un exemple, parmi tant d’autres, de la volonté de l’industrie à évoluer. « Pour ce faire, elle doit devenir davantage flexible, précise Stéphanie. Avant, une compétence avait une durée de vie de 20 ans. Désormais, les métiers et les technologies vont tellement vite, que si l’industrie ne s’adapte pas, elle risque de périr. Elle doit amener de nouvelles technologies et rapidement former ses équipes. »
« On aura toujours besoin d’améliorer l’industrie »
Et demain ? « L’industrie sera ultra connectée, répond Yohann. Elle exploitera la donnée pour améliorer la prédictibilité et gagner en performance. Elle ne sera pas dévolue, parce que nous avons toujours besoin d’enrichir les modèles numériques. Les scénarii d’utilisation d’une ligne, d’une machine ou d’une usine sont infinis. Nous aurons toujours besoin d’améliorer l’industrie ! »
Une industrie toujours plus technologique oui, mais pas déshumanisée, selon Stéphanie : « Le challenge de demain est de continuer toutes ces optimisations pour plus de performance industrielle, en ayant des hommes et des machines encore plus connectés, et qui travaillent ensemble. C’est la machine au service de l’humain et l’humain qui contrôle et donne le tempo. » Et de conclure : « La majorité des produits et infrastructures qui nous entourent aujourd’hui sont issus de l’industrie. Cette dernière devient de plus en plus sensible aux besoins humains et cherche à rendre notre quotidien plus agréable. Un bel exemple est celui de la création de prothèses pour les personnes ayant perdu un bras ou une jambe. L’industrie s’adapte au corps humain et personnalise également les schémas thérapeutiques. C’est une industrie au service de l’Homme. »
* Sous ensemble de l’intelligence artificielle (IA), le machine learning vise à apprendre aux machines à tirer des enseignements des données à s’améliorer avec l’expérience.
** Ou internet des objets, désigne le réseau collectif d’appareils connectés et la technologie facilitant leur communication ainsi qu’avec le cloud.
Views: 0